製造業におけるデジタルツインとは?活用シーンや成功に導く方法を紹介
製造業の技術者の皆様は、生産性向上とコスト削減の両立に日々頭を悩ませているのではないでしょうか。デジタルツインは、製造ラインの完全可視化と予知保全を実現し、生産性を30%以上向上させる可能性を秘めています。
本記事では、デジタルツインの具体的な活用シーンと導入手順を、先進企業の成功事例とともにご紹介します。IoTセンサーの選定からAIとの連携まで、現場で即実践できる情報が満載です。
デジタルツインが製造業の現場をどう変革するのか?5つの活用シーン
デジタルツインとAIの連携により、製造業の現場は大きく変わろうとしています。リアルタイムでの製造ライン監視から予知保全、品質管理の自動化、バーチャル製品開発、遠隔制御まで、生産性を飛躍的に向上させる5つの革新的な活用シーンをご紹介します。
- リアルタイムでの製造ライン完全可視化による異常の早期発見
- AIと連携した予知保全システムによる設備稼働率の最大化
- 品質管理の自動化による不良品発生率のゼロ化
- バーチャル環境での製品開発期間の大幅短縮
- 遠隔地からの製造ライン制御による働き方改革の実現
製造現場のデジタル化がもたらす具体的な効果と、その実現方法を詳しく解説していきましょう。
1. リアルタイムでの製造ライン完全可視化による異常の早期発見
デジタルツインによる製造ラインの可視化は、従来の目視点検では見落としがちな微細な異常も確実に捉えることを可能にします。3Dモデル上にリアルタイムデータを重ね合わせることで、製造現場の状況をより直感的に把握できるようになりました。
製造ラインの効率的な監視には、以下の3つの要素が重要な役割を果たします。
- 各種センサーとIoTデバイスによる24時間365日の常時モニタリング体制
- AIによる異常検知システムを活用した通常稼働パターンからの逸脱検出
- 過去の異常データとの照合による故障予兆の早期把握と予防保全の実現
この仕組みにより、従来は熟練作業者の経験と勘に頼っていた異常検知を、客観的なデータに基づいて実施できるようになります。異常の予兆を早期に発見することで、計画的なメンテナンスが可能となり、突発的な設備停止によるライン稼働率の低下を防ぐことができます。
さらに、異常発生時には関係者へ即座にアラートを発信し、迅速な対応を可能にします。これにより、問題が大きくなる前に適切な措置を講じることができ、製造ラインの安定稼働を実現します。
2. AIと連携した予知保全システムによる設備稼働率の最大化
デジタルツインとAIを組み合わせた予知保全システムは、製造設備の稼働状態を常時監視し、故障を未然に防ぐことで設備の稼働率を最大化します。従来の定期保守から、より効率的な予知保全へと進化を遂げています。
AIは機械学習により、センサーデータから設備の正常な動作パターンを学習します。わずかな振動や温度変化など、人間では気づきにくい異常の予兆も見逃しません。
デジタルツインは設備の3Dモデル上で劣化状態をシミュレーションし、AIと連携して部品の残存寿命を高精度に予測します。これにより、最適なメンテナンスのタイミングを事前に把握できるようになりました。
予知保全システムの導入による具体的な効果は以下の通りです:
導入効果 | 削減率 |
---|---|
年間保守コスト | 30%削減 |
計画外停止時間 | 80%削減 |
このように、デジタルツインとAIの連携は、設備保全の効率化と製造ラインの安定稼働に大きく貢献しています。
3. 品質管理の自動化による不良品発生率のゼロ化
デジタルツインとAIの連携による品質管理の自動化は、製造業における不良品問題を根本から解決する可能性を秘めています。高精度なセンサーとAIによる画像解析技術を組み合わせることで、製品の寸法や外観を0.1mm単位で自動検査できます。
人間の目では気づきにくい微細な品質異常も、AIが瞬時に検出して製造ラインにフィードバックします。これにより、不良品が出荷される前に予防的な対策が可能になりました。
検査項目 | 従来の目視検査 | AI検査 |
---|---|---|
寸法精度 | ±0.5mm | ±0.1mm |
検査時間 | 30秒/個 | 0.5秒/個 |
不良品検出率 | 85% | 99.9% |
さらに重要なのは、AIによる不良品発生パターンの分析です。製造条件をリアルタイムで最適化することで、品質のばらつきを最小限に抑制します。
蓄積された品質データをAIが分析することで、不良品発生の根本原因を特定。製造プロセスの継続的な改善につなげることで、限りなくゼロに近い不良品率の実現が視野に入ってきました。
4. バーチャル環境での製品開発期間の大幅短縮
デジタルツインを活用したバーチャル環境での製品開発は、従来の物理的な試作と検証のプロセスを大きく変革します。3Dモデル上で製品の挙動や性能を正確に再現し、様々な条件下でのシミュレーションを行うことで、実機での試作回数を従来の10分の1程度まで削減できます。
製品設計の変更点をデジタル空間で即座に検証できるため、設計から量産までのリードタイムを50%以上短縮することが可能です。従来は物理的な試作品を製作して検証する必要があったプロセスが、バーチャル環境で完結するようになりました。
評価項目 | 従来手法 | デジタルツイン |
---|---|---|
試作回数 | 10回以上 | 1-2回 |
設計変更検証 | 2-3週間 | 数時間 |
信頼性評価 | 3ヶ月 | 1ヶ月 |
さらに、極限環境や異常負荷など、実機での再現が困難な条件下でのテストもバーチャル空間で実施できます。これにより、製品の信頼性評価にかかる期間を従来の3分の1程度まで短縮し、より確実な品質保証を実現できます。
5. 遠隔地からの製造ライン制御による働き方改革の実現
デジタルツインを活用した遠隔制御システムにより、製造ラインの監視や制御が場所を問わず可能になります。VR/AR技術との組み合わせで、離れた場所からでも現場にいるかのような臨場感で作業状況を把握できます。
熟練技術者の知見や経験をデジタル化し、スマートデバイスを通じて全拠点でリアルタイムに共有することで、技術伝承の課題も解決できます。作業者はタブレットやスマートグラスを装着することで、熟練者からの遠隔指導を受けながら作業を進められるようになりました。
遠隔制御の主な効果 | 導入後の改善効果 |
---|---|
移動時間の削減 | 約70%削減 |
対応時間の短縮 | 約50%短縮 |
技術支援の範囲 | グローバル対応可能 |
さらに、時差のある海外拠点との24時間体制の製造ライン管理も実現可能です。各拠点の稼働状況をリアルタイムで把握し、必要に応じて遠隔で設備調整や不具合対応を行うことで、グローバルでの生産効率を最大化できます。
製造業のデジタルツイン化を成功に導く3ステップ
デジタルツイン導入の成功には、体系的なアプローチが不可欠です。IoTセンサーによるデータ収集基盤の構築から始まり、最適なプラットフォームの選定と段階的な導入を経て、現場スタッフの育成とデータ活用体制の確立まで。この3つのステップを着実に実行することで、製造現場の生産性向上を実現できます。
1. IoTセンサーとネットワークによるデータ収集基盤の構築
製造設備のデジタルツイン化の第一歩は、正確なデータ収集基盤の構築です。工場全体の稼働状況を把握するため、各設備に適切なIoTセンサーを設置し、ネットワークインフラを整備する必要があります。
生産設備の状態を正確に監視するには、以下の重要パラメータの測定が不可欠です。
- 温度・振動・電流値などの設備状態データ
- 生産量・稼働時間・不良率などの生産性データ
- 消費電力・エアー使用量などのユーティリティデータ
これらのデータを確実に収集するため、センサーの種類や設置位置は製造プロセスの特性に応じて慎重に選定します。また、データの信頼性を確保するためには、センサーの定期的な校正とネットワークの冗長化が重要です。
無線LANと有線LANを組み合わせたハイブリッド構成を採用し、通信障害時のバックアップ体制を整えることで、安定したデータ収集を実現できます。
2. デジタルツインプラットフォームの選定と段階的導入
デジタルツインプラットフォームの選定では、自社の製造工程の特性や目標に合わせた適切な評価基準の設定が重要です。導入に際しては、投資対効果を最大化するため、重要度の高い製造ラインから優先的に着手する段階的なアプローチが効果的です。
評価項目 | 選定のポイント |
---|---|
機能性 | リアルタイムデータ処理能力、シミュレーション精度 |
拡張性 | 他システムとの連携、カスタマイズ対応 |
運用性 | 使いやすさ、保守性、技術サポート体制 |
システム統合における技術的課題は、事前に詳細な洗い出しを行い、具体的な対応策を計画に組み込むことが大切です。既存システムとの連携や、データフォーマットの統一など、想定される課題への対策を事前に準備しましょう。
実装スケジュールは、3〜6ヶ月単位の実現可能な目標を設定し、各段階での成果を確認しながら進めることをお勧めします。この際、現場スタッフの意見も積極的に取り入れ、実務に即した導入計画を立案することが成功への鍵となります。
3. 現場スタッフの育成とデータ活用体制の確立
デジタルツインの効果を最大限引き出すには、現場スタッフの育成とデータ活用の体制整備が不可欠です。製造現場の知見とデジタル技術を融合させる人材の育成が、成功への重要な鍵となります。
現場スタッフの育成において重要なポイントは、以下の3つの要素です。
- データサイエンティストやシステムエンジニアの育成プログラムの確立と継続的な実施
- 現場作業員向けのデータ分析ツール活用トレーニングの実施と定期的なスキルアップ支援
- 製造現場とIT部門の定期的な情報共有会議の開催とナレッジ蓄積の仕組み作り
特に重要なのは、製造現場とIT部門の連携体制の構築です。双方の知見を活かしたデータ活用の仕組みを整備することで、より効果的な意思決定が可能になります。
また、データ活用の成果を可視化し、現場にフィードバックする仕組みも重要です。具体的な改善効果を実感できることで、スタッフのモチベーション向上にもつながります。
定期的な研修や勉強会の開催、成功事例の共有など、継続的な学習機会の提供も欠かせません。現場の声を反映させながら、実践的なスキル習得を支援する体制づくりを進めることが望ましいでしょう。
製造業DXの鍵を握るデジタルツインとAI・IoTの連携
製造現場のIoTセンサーから収集したビッグデータをAIで分析し、デジタルツインによって製造プロセス全体を可視化・最適化する取り組みが進んでいます。5Gの活用で超高精度なリアルタイムモニタリングを実現し、サプライチェーン全体の効率化も可能になりました。
- デジタルツインを支えるIoTセンサーとデータ収集の仕組み
- AIによる製造プロセスの自動最適化と予測分析
- 5G活用による超高精度なリアルタイムモニタリング
- サプライチェーン全体を可視化するデジタルツイン戦略
- 主要プラットフォームによる製造業向けソリューション
各種クラウドプラットフォームが提供する製造業向けソリューションと組み合わせることで、生産性の飛躍的な向上を実現できます。
デジタルツインを支えるIoTセンサーとデータ収集の仕組み
デジタルツインの精度と信頼性を左右する重要な要素が、製造現場に設置されたIoTセンサーとデータ収集の仕組みです。現場の状況を正確に把握するため、様々な種類のセンサーを適切に配置する必要があります。
IoTセンサーによって収集される主なデータと用途について、以下のように整理できます。
センサー種類 | 測定項目 | 主な用途 |
---|---|---|
振動センサー | 振動周波数・加速度 | 設備の異常予兆検知 |
温度センサー | 設備・製品の温度 | 品質管理・過熱防止 |
電流センサー | 消費電力・負荷状態 | 設備の稼働状況把握 |
これらのセンサーから収集されたデータは、エッジコンピューティング技術によって前処理された後、クラウド上のデータレイク基盤に集約されます。データの信頼性を確保するため、センサーの定期的な校正とネットワークの冗長化が不可欠です。
収集されたデータは、AIによる分析を経てデジタルツインにリアルタイムで反映され、製造現場の状況を正確に再現します。この仕組みにより、遠隔地からでも現場の状況を詳細に把握し、迅速な意思決定が可能になります。
AIによる製造プロセスの自動最適化と予測分析
デジタルツインとAIを組み合わせることで、製造プロセスの自動最適化が実現できます。AIが大量の製造データを分析し、品質や生産効率に影響を与える要因を特定していきます。
製造現場で収集された膨大なデータをAIが学習することで、以下のような最適化が可能になります:
- 製造パラメータ間の複雑な相関関係を解析し、最適な生産条件を自動導出
- 過去の生産実績データから、品質と歩留まりを最大化する制御値を自動設定
- リアルタイムデータと過去データの分析による異常予兆検知と早期対策の実施
- 需要予測に基づく生産計画の最適化と在庫の適正化
特に予測分析の分野では、機械学習モデルを活用することで、従来は熟練作業者の経験に頼っていた判断を、より正確かつ効率的に行えるようになりました。
さらに、AIによる最適化は24時間365日休むことなく継続的に実行され、製造プロセスの改善サイクルを加速させます。これにより、製品品質の向上と生産効率の最大化を同時に実現することが可能です。
5G活用による超高精度なリアルタイムモニタリング
5Gの超高速・大容量通信により、製造現場の監視能力は飛躍的に向上しています。従来の無線通信では難しかった数千個規模のセンサーデータを、わずか1ミリ秒未満の遅延でデジタルツインに同期できるようになりました。
高精細カメラで撮影した製品画像も、5Gネットワークを通じてリアルタイムに転送可能です。AIによる外観検査システムと組み合わせることで、品質判定の即時実行と不良品の早期発見を実現しています。
工場内の物流効率化においても5Gは重要な役割を果たします。以下のような具体的なメリットが挙げられます。
- モバイルロボットや自律搬送車(AGV)の位置情報を誤差1cm以内で把握
- 複数台のAGVを最適経路で制御し、衝突や渋滞を回避
- 作業進捗に応じた部品・製品の自動搬送で、待機時間を最小化
これらの技術革新により、製造現場全体の可視化とリアルタイムな制御が可能になりました。生産性向上とコスト削減を同時に実現する新たな製造基盤として、5G活用への期待が高まっています。
サプライチェーン全体を可視化するデジタルツイン戦略
サプライチェーンの効率化には、調達から製造、物流、販売までの一連の流れを一元的に把握することが不可欠です。デジタルツインを活用することで、これらの工程をリアルタイムで可視化できます。
製造業各社は、IoTセンサーやRFIDタグを活用し、原材料の在庫状況や生産ラインの稼働状況、物流拠点での在庫量などを常時モニタリングしています。これらのデータをクラウド上のデジタルツインに集約することで、サプライチェーン全体の最適化が可能になります。
工程 | デジタルツインによる可視化効果 |
---|---|
調達 | 原材料の在庫状況把握と適正発注量の自動算出 |
製造 | 生産ラインの稼働状況分析とボトルネックの特定 |
物流 | 在庫量の最適化と配送ルートの効率化 |
特にグローバルに展開する企業では、世界各地の拠点の状況をリアルタイムで把握し、需要変動に応じて生産計画を柔軟に調整できる体制の構築が重要です。デジタルツインを活用した可視化戦略は、このような課題解決の有効な手段となっています。
主要プラットフォームによる製造業向けソリューション
製造業向けデジタルツインの実現には、主要クラウドプラットフォームが提供する包括的なソリューションが不可欠です。市場をリードするMicrosoft AzureとAWS IoTは、それぞれに特徴的な機能を備えています。
プラットフォーム | 主な特徴 | 強み |
---|---|---|
Microsoft Azure | 製造業向けテンプレート豊富、Power BIとの連携 | 導入実績多数、手厚いサポート体制 |
AWS IoT | IoTデバイス管理機能充実、ML連携容易 | スケーラビリティ高、コスト効率的 |
プラットフォーム選定では、既存システムとの親和性や、業界標準規格への対応状況を重視する必要があります。特にOPC UAやMTConnectといった製造業標準プロトコルへの対応は、システム統合の容易さを左右する重要な要素です。
導入時のコスト試算では、初期費用に加えてデータ転送量やストレージ使用量に応じた従量課金、保守・運用費用まで含めた総所有コストを検討することが望ましいでしょう。
各プラットフォームは、APIを通じたサードパーティ製品との連携も強化しており、既存の生産管理システムやMESとの統合も容易になっています。
デジタルツインの制作なら株式会社Advalayがおすすめ
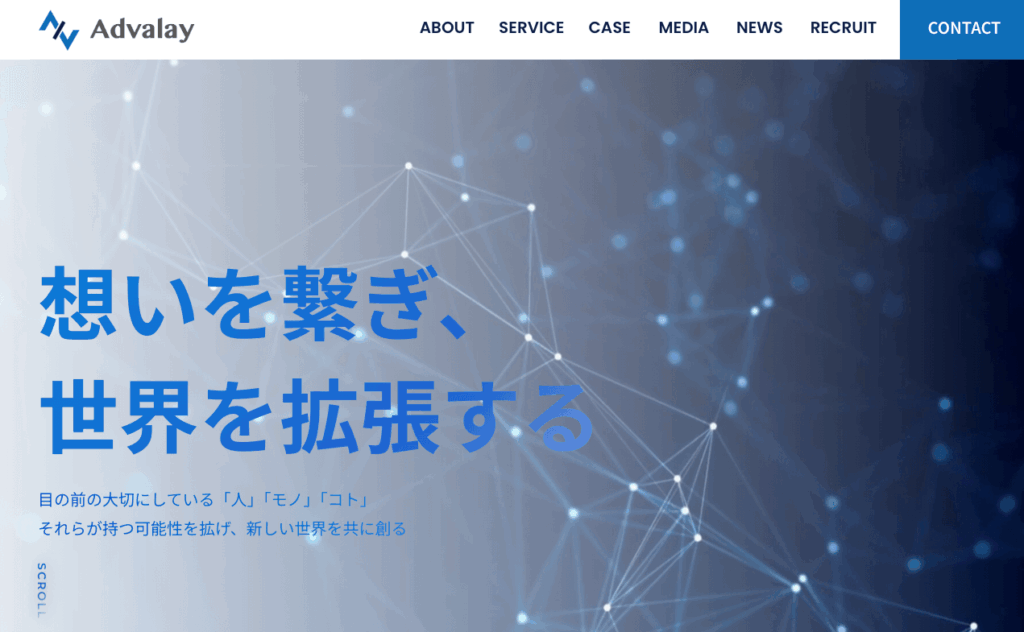
株式会社Advalayは、デジタルツイン制作において高い技術力と豊富な実績を誇ります。製造業や建設業、医療など多様な分野で成功事例を持つ同社は、AIやIoT、ビッグデータを活用したオーダーメイドのソリューションを提供します。特に、専門知識を持つエンジニアチームが顧客ごとにカスタマイズ対応を行う点が強みです。
デジタルツイン制作会社は多く存在しますが、Advalayは幅広い業界対応力や最新技術の導入、透明性のある料金体系といった面で優れています。他社が提供する一般的なテンプレートサービスとは異なり、Advalayは顧客ごとに最適化されたオーダーメイドのモデルを制作することで、より高い成果を実現します。
また、設計から運用、サポートまでの一貫した対応により、初めて導入する企業でも安心してプロジェクトを進められるのも大きな強みです。最新のAI技術やIoTデータを取り入れ、他社にない付加価値を提供しています。
まとめ
デジタルツインは製造現場のあらゆるデータをリアルタイムで可視化し、生産性向上を実現する革新的なソリューションです。本記事では、導入事例や具体的な効果、実装のポイントを解説しました。
今後の製造業のデジタル変革において、デジタルツインの活用が重要な鍵となることが分かります。
この記事を読んだあなたが、製造業でデジタルツインを効果的に活用できるきっかけが作れたら嬉しく思います。